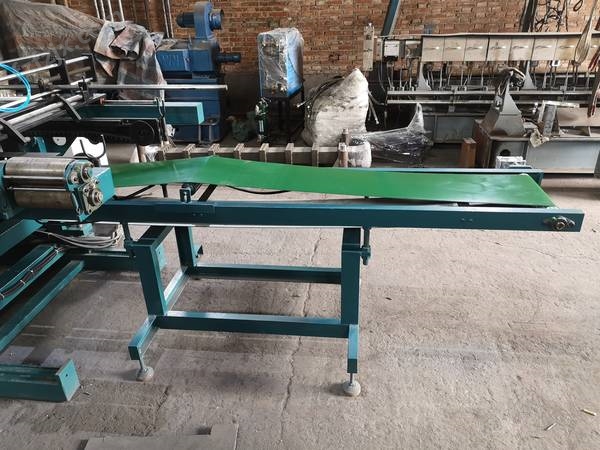
一、功能特点
1.机械气动,电气一体化各动作协调完整程序:PLC控制,显示频操作简单方便。
2.挤出机物料进入压延机二辊定型,使成型制品得到了相应的二次成型制品的美观要求。
3.压延辊配备有间隙微调节机构使制品厚薄度与克重达到所要求制品的克重。
4.两辊定型补偿温度备有油模温机智能控制模片温差,操控使用方便简捷稳定。
5.变频器驱动,稳定的链输送压延后模片,及成型后制品,线达到18.6米分。
6.两条锻件制作的输送的链轨,经高速耐磨钢加工制成,宽度大小可调,调节方便可供不同大小的模具进行成型工作。
7.平移合模工作台,双向行程可调,使成型的动作时间得到缩短,同时也使模具的成型高度得到了合理的位置。
8.平移的同步协调动作,是由变频器驱动,来完成,平移的工作速度,经程序PLC设置完成高要求的压延辊,链输送的同步线速。
9.合模工作台双向行程由电磁阀驱动气缸进行上下合模动作。
10.4KW水环式真空泵供使,成型2次吹气,脱膜,延时真空。
11.在线切割纵向由两把高速钢切割刀配由上下机械调节机构,完成切割的工艺要求,横向由气动电磁阀时间控制器,来自操作切割气缸的横向动作及气缸的上下切割。
12.切割下来的每板产品经设置计数器设定所要切割后产品的数量,达到所要冲材的张数。
13.纵向切割出来的边料,经边料粉碎机的牵引进行边料的粉碎,由粉碎机物料输送挤出机落料口进行循环使用。
14.产品输出步进式工作,输送所需的长度可调,产品输出直至冲材机完成整机成型产品的制作工艺。
二、工艺流程
挤出→压延定形→链输送→平移成形→在线切割→计数堆叠→输送→冲裁→成品
三、 技术参数
1、适应模具宽度:400-600mm。
2、制作成型产品的厚度:0.25-1.2mm。
3、合模行程:160 mm。
4、成形面积:600×700 mm。
5、成形高度:60 mm。
6、成形深度:60mm。
7、工作效率(次/分钟)8-24(模具大小来计模次)
8、制品定形冷却。
9、汽源外配:供气量:12.0m /min, 气压(Mpa)0.8。
10、耗水量:4-5Cube/Hour。
11、真空外置:气量12.0m /min。
12、使用电源,三相四线制 380v/220v/50Hz。
13、补偿加热功率:9 kw。
14、压延定形驱动功率:4 kw。
15、整机功率:18.5 kw。
16、外形尺寸(lxwxh):5000×2000×11250。
17、辊规格; 直径240mm×长度800mm